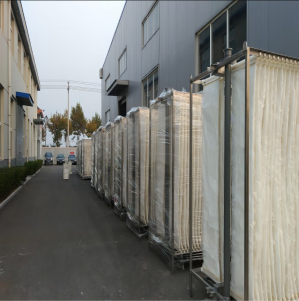
The textile industry is known for its high water consumption and significant wastewater generation, which often contains a variety of pollutants, including dyes, chemicals, and other organic and inorganic substances. Addressing the environmental challenges posed by this wastewater is crucial for sustainable industry practices. One of the most effective solutions for treating textile processing wastewater is the use of Membrane Bioreactor (MBR) membranes.
What is MBR Technology?
MBR technology integrates a biological treatment process with membrane filtration. In this system, microorganisms break down organic pollutants in the wastewater, and then membrane filtration separates the treated water from the remaining sludge and contaminants. This combined process ensures the production of high-quality effluent that can be safely discharged or reused in various applications.
Benefits of Using MBR Membranes
1. High-Quality Effluent: MBR systems provide exceptional filtration, removing suspended solids, microorganisms, and a broad range of pollutants. The resulting effluent meets or exceeds strict environmental standards, making it suitable for reuse in industrial processes, irrigation, or even as potable water in some cases.
2. Compact Footprint: Compared to traditional wastewater treatment methods, MBR systems have a smaller footprint, making them ideal for textile processing facilities where space may be limited.
3. Consistent Performance: MBR systems offer reliable performance even with fluctuating wastewater compositions and flow rates, which are common in textile processing operations.
4. Reduced Sludge Production: The biological processes in MBR systems generate less sludge compared to conventional methods. This reduces the costs and environmental impact associated with sludge handling and disposal.
5. Energy Efficiency: Modern MBR systems are designed to be energy-efficient, which helps in reducing the overall operational costs.
Implementing MBR Technology in Textile Processing
The process of integrating MBR technology into textile wastewater treatment involves several steps:
1. Pre-Treatment: Initial screening and removal of large particles to protect the MBR membranes from damage.
2. Biological Treatment: Microorganisms degrade organic pollutants in the wastewater.
3. Membrane Filtration: The treated water passes through MBR membranes, which filter out remaining contaminants.
4. Post-Treatment: Additional treatment steps, if needed, to ensure the water meets specific quality standards.
Real-World Applications and Success Stories
Several textile processing facilities around the world have successfully implemented MBR technology, demonstrating its effectiveness and benefits. For instance, a textile dyeing plant in Bangladesh reported a significant improvement in wastewater quality and operational efficiency after installing an MBR system. Similarly, a garment manufacturing facility in Vietnam achieved compliance with stringent environmental regulations and reduced operating costs by adopting MBR membranes.
Conclusion
The use of MBR membranes in treating textile processing wastewater offers numerous advantages, including the production of high-quality effluent, space efficiency, consistent performance, reduced sludge production, and energy efficiency. As the textile industry continues to seek sustainable and cost-effective wastewater treatment solutions, MBR technology stands out as a highly effective option. By adopting MBR membranes, textile manufacturers can improve their environmental performance and achieve long-term economic benefits.
Promoting the adoption of MBR technology in the textile industry is essential for addressing the environmental challenges associated with textile processing wastewater. Through continued innovation and commitment to sustainability, the textile industry can move towards more environmentally responsible practices and a greener future.