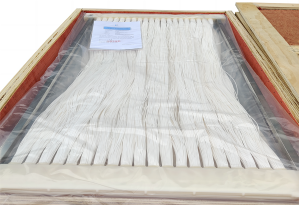
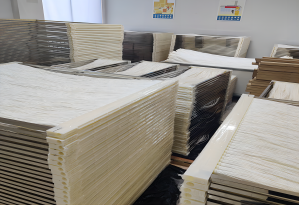
Fouling is the process by which the particles (colloidal particles, solute macromolecules) are deposited or absorbed onto the membrane surface or pores by physical and chemical interactions or mechanical action. Membrane fouling can cause severe flux drops and affects the quality of the water produced. Severe fouling may require intense chemical cleaning or membrane replacement. This increases the operating costs of a treatment plant.
A recent review reports the latest findings on applications of aeration in submerged membrane configuration and describes the performance benefits of gas bubbling. The choice of aeration rate is a key parameter in submerged membrane bioreactor design.
Many other antifouling strategies can be applied in membrane bioreactor applications. They include, for example:
· Intermittent permeation or relaxation, where the filtration is stopped at regular time intervals before being resumed. Particles deposited on the membrane surface tend to diffuse back to the reactor; this phenomenon will be increased by the continuous aeration applied during this resting period.
· Membrane backwashing, where permeate water is pumped back to the membrane and flows through the pores to the feed channel, dislodging internal and external foulants.
· Air backwashing, where pressurized air in the membrane's permeate side builds up and releases a significant pressure within a very short period of time. Membrane modules, therefore, need to be in a pressurized vessel coupled to a vent system. Air usually does not go through the membrane. If it did, the air would dry the membrane and a re-wet step would be necessary, accomplished by pressurizing the feed side of the membrane.
· Proprietary antifouling products, such as Nalco's Membrane Performance Enhancer Technology.